- ホーム>
- 初めて基板分割機をご検討される方
基板の生産効率を上げる為1枚のシート基板に複数の製品基板を配列し同時に多数の基板を製作します。
完成した基板を個々に分離する工程を基板分割と言います。
当初基板は分割を行い易くする為両面よりV溝を掘り込み、作業者は基板を手に持ち逆Vガイド台にV溝位置を当て手作業にて分割を行っておりました。この結果分割時に発生するストレスが非常に大きく実装部品のハンダ剥離又は基板ひび割れによるパターン切断などが発生しやすく、作業性の向上のみを目的としておりました。
その後これらの不良によるトラブルが表面化し、分割時の品質を確保しながら分割を行う装置類が必要とされはじめました。
[注意]
1、ストレスとは基板を分割する際に発生するわずかな変形を言います
2、逆Vガイド方式での発生ストレスはおおよそ5000〜7000マイクロストレイン程度といわれております。
基板分割を行う方法としてはルーター分割・ダイシング分割・プレス分割等が普及しております。
TMEではこの内ルーター分割、プレス分割更に押し切り分割〔卓上分割機〕の装置の製作を行っております。
分割方法 |
概要 |
---|---|
ルーター分割方式 | 基板分割用のルータービットツールを使用します、このツールを高速回転させ分割をすべく指定位置を分割します、分割位置は制御部に記憶させ基板の機種により座標データを呼び出し多種類の基板に対応します。 |
ダイシング分割方式 | 薄い砥石を高速回転させ指定位置を切断します、分割位置は制御部に記憶させ基板の機種により座標データを選択し多種類の基板に対応します。 |
プレス分割方式 | 基板の分割位置に合わせて分割用の刃を組み込んだ分割型により分割を行います。 |
押し切り型分割方式 | 上記分割装置類はいずれも量産を目的として製作されております、生産数が少なくV溝基板分割対応用として製作、上下の回転する円形刃の間に基板を通し極小の刃間隔のスキマにより分割します、分割時に発生するストレスはやや大きく、手軽に使用できるので普及しております。 |
ルーター分割装置の場合
ルーター分割方式の良い点
・縦・横更に斜め方向でも分割が可能。
・0・4〜1・6mm程度の厚さで有れば対応が可能。
・ツール価格が安価 ツール径に関係なく1本200円
・分割座標を装置に記憶させ簡単に基板の機種変更が簡単である
〔タッチパネルにて座標データを選択し直
し・分割ジグを交換します、段変え時間は約2分位〕
・ストレスの発生量が少ない 50〜130マイクロストレイン〔分割端面位置より1mm程度離れた位置で測定の場合〕
ルーター分割方式の欠点
・発生する粉塵が多い
・実装部品高さに限界がある
・位置決め用ジグが必要である
・分割速度が比較的遅い為主にミシン目構造の基板が対象基板となります
スピンドル先端部分の形状
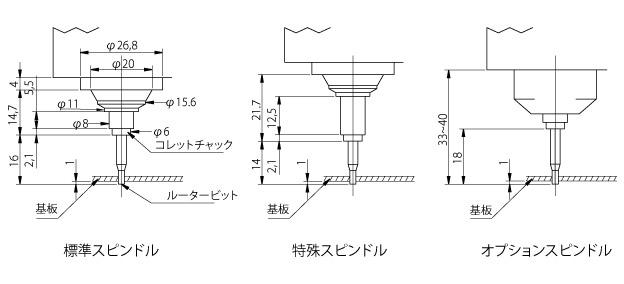
分割速度及びツール回転数はどの位?
分割速度
0・8mm=6・7mm/s 1・0mm=13・4mm/s 1・2mm=16・6mm/s
1・5mm=18・4mm/s 1・6及び2・0mm=20・0mm/s
ツール回転数
0・8及び1・0mm=40,000r/m 1・2mm=35,000r/m
1・5mm=29,000r/m 1・6mm=27,000r/m 2・0mm=23,000r/m
ツール寿命はどの位?
連続使用で約8〜10時間位。
ツール寿命の延長方法
ツールの同一箇所にて連続切削を行う為刃の一部分のみ磨耗します。
ツール高さの切換を行い新しい刃部分にて分割を行うことによりツールの寿命の延長を行っております。
方法としてZ軸の下降端高さの切り替えをエアー駆動、又はサーボモーター駆動にて行う2種の方法を製作しており, エアー駆動の場合、切り替え高さは2mmの切り替えが1回のみとなっております、結果ツール寿命を2倍に延長が可能です、製作費が安価な点がメリットです。
サーボモーター駆動の場合の切り替え高さは数段階の切り替えが可能、ツール寿命を数倍に延長が可能となります。切り替え高さが数段階にする点、又は切削高さを変更できる点がメリットとなります。
分割用ジグの使用目的は?
分割時基板を拘束し分割位置精度を確保します。
例えば1個片が5カ所の接続部でつながっていた場合1カ所部分から5カ所部分に順次分割が進み後ろの方の分割をした際に個片が向きを変え分割指定位置以外を分割することがある為基板の拘束が必要となります。
粉塵の集塵は上面・下面いずれか?
上側集塵構造の場合ツール寿命の延長の働きに不都合が出やすくなります。
弊社は全機種下側集塵構造となっております。
分割時に発生する粉塵・その対策
ルーター分割は高速回転させたヤスリ風ツールにより基板を削ることにより分割を行います。
その結果細かい粉塵が発生し基板に対し良くない影響を与えます。
大容量の集塵装置更に分割用ジグに粉塵をとり易くする構造を施します。
基板全面に対し下面より同時に吸引を行う方法あるいは分割部分の下位置に粉塵吸引用穴を設け局部吸引を行います。基板全面吸引方式のジグ製作費は比較的安価に製作が出来、局部吸引方式の場合は構造が複雑となる為製作費が高価となります。
又基板全面吸引の場合集塵装置が大型となり、局部吸引の場合は小型集塵装置で可能となります。
どちらの構造にするかは基板の実装状態により選択します。
旋回テーブル組み込み型とは?
分割ジグへの基板の出し入れ位置と分割を行う位置を旋回テーブル上2箇所に設けることにより、分割時に別位置で基板の出し入れを行うことができます。
結果装置の生産時間としては分割時間+テーブル旋回時間だけとなり基板の出し入れ時間は0となります。
分割時間をより短縮することが可能です。
2スピンドル構造とは?
分割時間をより短縮させる為1枚の基板に対し2台のスピンドルにより2個片を同時に分割を行います
スピンドル間隔は可変構造となっており、片側のスピンドルは分割ポイント毎に分割又は分割ナシの設定が出来ることにより幅広く種々な基板に対応が可能、1スピンドル構造の時間に対し約2倍弱の分割速度の向上が可能となります。
インライン方式〔自動分割〕のルーター分割装置
同じ機種の基板を大量に分割するにはインライン型機種が向いております。
上流から搬送コンベアーで送られてきた基板を分割後端材部分を投棄し個片となった基板を種々な方法で下流に排出します。
[下流への排出方法]
下流への排出方法は客先のライン構成に合わせ数種類が考慮されています。
標準仕様の場合は分割個片全数を同時にチャックし排出用平コンベアー上に降ろします。
他に基板両端3mm部分を受ける巾可変式のベルトコンベアーにて水平に次の工程に送り出す方法個片形状が上記コンベアーで受けられない場合は1個片ずつを受け渡しジグ上に降ろしジグごと装置の外位置まで送り出し次の工程に受け渡します,この受け渡し動作は主にロボットを使用するものとします。
更に搬送トレー上にパレタイズ動作による排出方法があります、この場合分割全数を同時にトレー上
に降ろす、又は1個ずつトレー上に降ろし複数回搬送動作を行う等の方法 があります。トレー上セットの場合はトレーの搬送・位置決めなどを行う為のトレーチェンジャーが必要となります。
客先トレー寸法に合わせたトレーチェンジャーの製作も行います。
ルーター分割でのトラブルは?
・分割時ヒゲと称する基板の繊維が分割面に出る場合があります。
対応策としてはヒゲ発生面に対し0・1mm程度の追い込みによる2回切削を行うことにより減らすことが可能です。
・分割面にツノと称する突起状が残る場合があります。
原因はツールの回転方向に対し切削送り方向が原因と思われます。
ツールの送り方向を時計回転方向に送ることにより防ぐことが可能です。
・ツール折れ
基本的にツールメーカーの指定する回転数及び送り速度で分割を行った場合はめったにツールが折れることはありません。
長距離の分割を行った場合は切削抵抗が原因となりスピンドルの回転が下がり、送り速度はそのままの為ツール折れが発生します。
取り合えずの対応策としてはスピンドル回転数を上げることによりツール折れを防ぐことが可能です。
この他にスピンドルに組み込まれておりますベアリングが磨耗し回転抵抗が原因で回転数が下がる場合もあります。この場合はスピンドルを交換することにより復元します。
TME製のルーター分割装置の場合回転数を常時監視し設定回転数に対し一定の割合で回転数が下がった場合警報を出し自動運転を停止いたします。
プレス分割の場合
プレス分割方式の良い点
・1ショットで1枚の分割箇所全数を同時に分割する為分割速度が速い。
・実装部品の高さが高くても対応が出来る。
・縦・横更に斜め方向でも分割が可能。
・V溝、ミシン目構造基板でも分割が可能。
・分割時に発生する粉塵が少ない。
・大量生産に向いている。
・磨耗した分割型は再研磨が可能。
プレス分割方式の欠点
・分割用型を必要とし製作費が高額である。
・分割時に発生するストレスが大きい。 500〜1000マイクロストレイン
実装部品に対し分割位置はどの位いまで接近が可能か?
実装部品から0・5mmまでは実績があります。
実装部品高さはどのくらいまで可能か?
上下面とも最大50mm位間では実績があります。
対応可能な基板材質
FR−4、コンポジット、紙フェノール等は実績があります。
[分割方法]
・向かい刃構造
上下2枚の分割刃を接近させ分割を行います、分割時のストレスは他の刃構造に対し比較的少ない。
・パンチ抜き構造
薄い基板又はミシン目巾位置を抜く場合に使用、分割時のストレスは向かい刃構造に比べやや多い。
・ビク抜き刃構造
フレキ基板の分割に使用、市販トムソン刃を組み込む為製作費が安価
分割型の寿命はどの位?
約30万ショット位です〔但しビク抜き型は含まれず〕
分割刃の材質は?
SKH51〔向かい刃構造の場合〕、超鋼又はSKH51〔パンチ抜き構造の場合〕
プレス出力の発生方法は?
エアー圧力を油圧に変換しこれをブースターにより高圧の油圧とし油圧シリンダーを作動させます。
油圧用オイルの寿命は?
弊社実績では3年くらいで補給をしております。
ストレスを低く分割を行う方法は?
・ストレスの影響を受ける実装部品から分割箇所を遠ざける。
・分割箇所を直線状に並べずストレスの相互干渉をよける為チドリ状に並べる。
押し切り分割の場合〔卓上分割機〕
卓上分割機を使用する理由
両面V溝基板の分割を主な目的とする分割機です。
本格的なルーター分割・プレス分割では初期投資が掛かりすぎ、生産数もあまり多くない場合に向いております。
分割刃は使い捨てか?
弊社で再研磨を行っております。
分割刃の刃先構造は特注構造が可能か?
客先の希望に応じて特注刃先構造を製作いたします。
基板厚さが薄くても対応が可能か?
基板厚さにより下記対応をとっております、但し両面V溝基板の場合とします。
0・8〜1・0mmの場合
刃の組み合わせをシャーリング風分割として対応しております。
0・4〜0・8mmの場合
専用分割刃を製作し対応します。
刃の寿命はどのくらい?
1日フル分割を行った場合約4ヶ月くらいです。
ストレス発生量はどのくらい?
分割端面から3mm程度離れて約500〜800マイクロストレイン程度です。
対応可能な基板材質
ガラエポ、コンポジット
[注意]
この方式の場合紙フェノールの分割は適しておりません。