- Home>
- Person who examines substrate division machine for the first time
Two or more product substrates are arranged to one seat substrate to raise the productive efficiency of the substrate and a lot of substrates are produced at the same time.
The process of individually separating the completed substrate is called substrate division.
The substrate was divided easily at first and the worker ..including V ditch..
was dividing from both sides to do into possession reverse-V guide stand of the substrate in the hand by V ditch position's the application person working. As a result, the stress that occurred when dividing generated the solder flaking off of the surface-mounted component or the pattern cutting by the substrate crack,
etc. easily very greatly, and aimed only at the improvement of the working efficiency.
The trouble due to these defects came to light, and devices that divided while securing the quality when dividing began to be needed afterwards.
[ Attention ]
I call slight transformation to occur when I divide a board the stress
The outbreak stress by the reverse V guide method is quite called 5000-7000 μs degree.
The router division, the dicing division, and the press division, etc. are widespread as the method of dividing the substrate.
In addition, the router division and the press division produce the device of the facing out division 〔 desk-top division machine 〕 among these in TME.
Approach to decomposition
|
Outline
|
---|---|
Router division method | The router bit tool for the substrate division is used, a specified position is divided to high-speed rotate this tool and to divide, and it ..coordinate data.. corresponds to calling many kinds of substrates by the memory in the control part and ..division position.. model of the substrate. |
Dicing division method | A thin whetstone is high-speed rotated, and the division position in which a specified position is cut is selected coordinate data and corresponds to many kinds of substrates according to the model of the substrate the memory in the control part. |
Press division method | It divides according to the division type that builds in the blade for division according to the position where the substrate is divided. |
Facing out type division method | There is little number of the production that above division devices are aimed for a mass production both, and is produced and the stress to occur at the time of the division dividing through a board between production, the turning circle blades of the top and bottom as application vs. the V-groove board division by the gap at a very small blade interval is slightly big and spreads because I can use it easily. |
For the router division device
Point where router division method is good
・Length and, in addition, side can divide for diagonal one.
・0.4It is possible to correspond if the thickness of - about 1.6mm and
existing.
・200 yen each regardless of the cheap tool diameter. the price
of the tool
・The division coordinates are memorized in the device and the model change
in the substrate is easily easy.
〔The steps changing time to exchange the selection do over again and the
division jig is about two quantiles in the touch panel as for coordinate data
〕
・The amount of generation of the stress is a little 50-130 μ s.
〔 position left from division edge side position by about 1mm measurement
〕
Fault of router division method
・The generated dust is abundant.
・There is a limit in the height of the mounting parts.
・The jig for positioning is necessary.
・Because the division speed is comparatively slow, the substrate of the
perforated line structure chiefly becomes an object substrate.
Shape of spindle tip
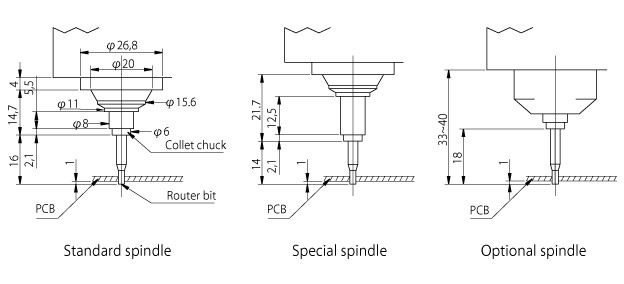
Which places are the division speed and the tool rotational speed?
Division speed
0.8mm=6.7mm/s 1.0mm=13.4mm/s 1.2mm=16.6mm/s
1.5mm=18.4mm/s 1.6 and 2.0mm=20.0mm/s
Tool rotational speed
0.8 and 1.0mm=40,000r/m 1.2mm=35,000r/m
1.5mm=29,000r/m 1.6mm=27,000r/m 2.0mm=23,000r/m
Which place is the tool longevity?
For about 8-10 hours in continuous use.
Method of extending tool longevity
To cut continuously in the same part of the tool, only a part of the blade
is worn out.
The longevity of the tool is extended by changing the height of the tool and
dividing in a new cutting portion.
Two methods of switching the height of the descent edge of Z axis as a method
by the air drive or the servo motor drive are produced, and the point where
the output cost is cheap is an advantage in the height of the switch in which
the result tool longevity only once the switch of 2mm can be extended to twice
in case of the air drive.
Possible the switch of several step floor, and ..several time.. extending the
tool longevity become possible the height of the switch at the servo motor
drive. A point that the height of the switch is made several step floor and a
revokable point of the height of cutting become advantages.
The use of jig for division?
The substrate is restrained when dividing and the division position
accuracy is secured.
For instance, for piece [hen] might change front and to divide excluding the
division specification position when division advances from one-place part
toward five-place part one by one when connecting by the joint whose throw
splinter is five places and the back was divided, the restraint of the
substrate is needed.
About the collection of dust, it is the upper surface and is either of lower side.
It becomes easy for the inconvenience to go out for the extension of the
tool longevity to work for the upside collection structure.
Our company is all model lower collection structure.
Dust and the measures generated when dividing
I divide the router division by sharpening a board by the high speed file style tool which I turned.
As a result, small mine dust occurs and has influence that I am not good for a board.
I take structure to make it easy to take the mine dust to a jig for division in large-capacity collector watches of the night.
I establish the hole for mine dust absorption at the lower position of a method absorbing at the same time from a lower part for the board entire surface or the division part and absorb a part. Production is made comparatively cheap as for the jig production costs of the board entire surface absorption method, and production costs become expensive so that structure becomes complicated in the case of the part absorption method.
In addition, a collector becomes large in the case of board entire surface absorption and becomes possible with a small collector in the case of the part absorption.
I choose which structure I make it by the implementation state of the board.
What is the swiveling table built-in type?
When dividing by installing the position where the substrate is put in and
out and the divided position to the division jig in two places on the turn
table, the substrate can be put in and out at another position.
The time of putting in and out of the substrate becomes 0 as production time
of the result device only at division time + table turn time.
The division time can be shortened more.
What is two spindle structure?
I divide two pieces by two spindle oil for one piece of board at the same
time to let you shorten division time more.
The spindle oil space becomes the variable structure, and I am wide, and
correspondence is possible, and, as for the spindle oil of the one side,
improvement of about a little less than 2 times division speed is enabled
on a board in various ways for time of one spindle oil structure because
it is possible for the division or the setting of the division pear every division point.
Router division device of in-line method 〔 automatic segmentation 〕
An in-line type model is suitable to divide the board of the same model in large quantities.
I drain the board which I dump division end materials part with the board which has been sent with a transportation conveyer, and became a unit piece from the upper classes by a method downstream in various ways.
[A discharge method to the down stream]
As for the discharge method to the down stream, several kinds are considered to the line constitution of the in front of the visitor.
I do a zipper of a division unit piece all quantity in the case of the normal specifications at the same time and take it down on a discharge use flat conveyer.
This transfer movement that I transfer by one piece to the next process horizontally when method unit piece shape to send out is not received with an above conveyer and take it down on a jig in the belt conveyor of the width variable expression to receive board both ends 3mm part elsewhere and send every jig out outside a device to the position and transfer to the next process shall use a robot mainly.
Furthermore, there is a method I transport it several times I take down this case division all quantity having a discharge method by the Pare Ta'izz movement on a transportation tray on a tray at the same time or and I take down by one on a tray, and to work. A tray changer to perform transportation / positioning of the tray is necessary in the case of the set in a tray.
I perform the production of the tray changer which I matched with in front of the visitor tray dimensions.
The trouble in router division?
・There is the case that the fiber of the board which calls itself a mustache at division time appears in the division side.
I can reduce it by performing twice cut by the spurt of around 0.1mm for a countermeasure for mustache outbreak side.
・There is the case that the umbonation which calls itself a horn in the division side is left.
As for the cause, a cut forwarding direction seems to be a cause for the rotatory direction of the tool.
I can prevent it by sending the forwarding direction of the tool to clock rotatory direction.
・Break a tool
There cannot be number of revolutions to appoint and the thing that a tool rarely compromises when I send it and divided it at a speed of the tool maker basically.
When I divided it, cut resistance becomes the cause that long-distance, and the turn of the spindle oil falls, and, as for the forwarding speed, sake tool buckling up as is occurs.
I can prevent tool buckling up by raising spindle oil number of revolutions for the countermeasure that I can scramble for.
In addition, there is it when bearing incorporated in spindle oil is worn, and number of revolutions falls for rotary resistance. In this case I am restored to the original state by changing spindle oil.
When I always watch number of revolutions in the case of a router division device made by TME, and number of revolutions fell down in a constant ratio for setting number of revolutions, I start a warning and stop automatic driving.
At the press division
Point where press division method is good
・Division speed is fast to divide one piece of division point all quantity by one shot at the same time.
・It is possible to correspond even if the height of the surface-mounted
component is high.
・Length and, in addition, side can divide for diagonal one.
・It is possible to divide even by V ditch and a perforated line structural
substrate.
・The dust generated when dividing is a little.
・It is suitable for mass production.
・The division type worn out can be ground again.
Fault of press division method
・The type for division is needed and the output cost large amount of
money.
・The stress that occurs when dividing is large. 500〜1000μs
Which place [imade] approach is possible compared with the surface-mounted component as for the division position?
There are results from the surface-mounted component to 0.5mm.
Even how much is possible as for the height of the mounting parts?
There are results among upper and lower sides and about 50mm or less.
Substrate material that can correspond
FR-4, the composite, and the paper phenol, etc. have results.
[ Approach to decomposition ]
・The blade structure toward.
Upper and lower two division blades are made to approach and the stress when
separately dividing is comparatively few compared with other blade structures.
・Punch pulling out structure
When I outrun being located, use, the stress at the time of the division leave and compare it with blade structure, and there is slightly many a thin board or perforation width.
・Blade structure without fish basket
Production costs are cheap to incorporate use, commercial Thompson blade in the division of the FPC board.
Which place is the longevity of the division type?
About 300,000 shot title. 〔But the model without fish basket is not included〕
The material of division blade?
SKH51 〔 blade structure of facing 〕 and super-steel or SKH51〔 punch pulling out structure 〕
The method of generating press output?
The air pressure is converted into the oil pressure, this is assumed to be an oil pressure of the high pressure by the booster, and the oil hydraulic cylinder is operated.
The longevity of oil for oil pressure?
It replenishes it in our results in about three years.
The method of dividing stress low?
・The division part is kept away from the surface-mounted component in
which the influence of the stress is received.
・Not to arrange the division part straight and to avoid the mutual
interference of the stress, it arranges it like the plover.
At the facing out division〔 desk-top division machine 〕
Reason to use desk-top division machine
The division machine that aims at the division of both sides V ditch
substrate mainly.
It turns when an initial investment hangs too much in real router division and
the press division, and there are not too much a lot of numbers of production
either.
Is the division blade disposable?
Our company grinds again.
As for the tip of the blade structure of the division blade, is the custom-designed structure possible?
I will produce the custom-designed tip of the blade structure according to the customer's hope.
Even if it is thin that the substrate thickness, is correspondence possible?
However, the substrate thickness, the following correspondence is taken, and it makes it to the case of both sides V ditch substrate.
For 0.8-1.0mm
It corresponds as shirring style division the combination of blades.
For 0.4-0.8mm
The special division blade is produced and it corresponds.
How much is the longevity of the blade?
About four months when dividing full on the first.
How much is the amount of the stress generation?
It leaves the division edge side by about 3mm and about 500-800 μ s level.
Substrate material that can correspond
[Garaepo] and composite
[ Attention ]
The division of the paper phenol is not suitable for this method.